Savantec cylindrical rolling cutter includes rigid cylindrical rolling cutter and flexible cylindrical rolling cutter (see Figure 1 above for rigid cylindrical single wheel rolling cutter and Figure 2 for flexible single wheel cylindrical rolling cutter). The flexible cylindrical rolling cutter adds a flexible mechanism into the rolling cutter to protect the rolling cutter and know the rolling force when the outer circle jumps. Avoid damaging workpieces and tools.
The following is an introduction to the principle and application knowledge of rolling processing. You can choose to skip it.
Rolling is a non cutting plastic processing method. The rolling tool (rolling head) rolls the metal surface with high hardness rollers to produce plastic flow, which is filled into trench to reduce the roughness value of the metal surface (improve the finish), cold harden the surface structure and refine the grains, form dense fibrous shape, form a residual stress layer, and enhance the hardness and strength, So as to improve the wear resistance, corrosion resistance and fatigue strength of metal surface.
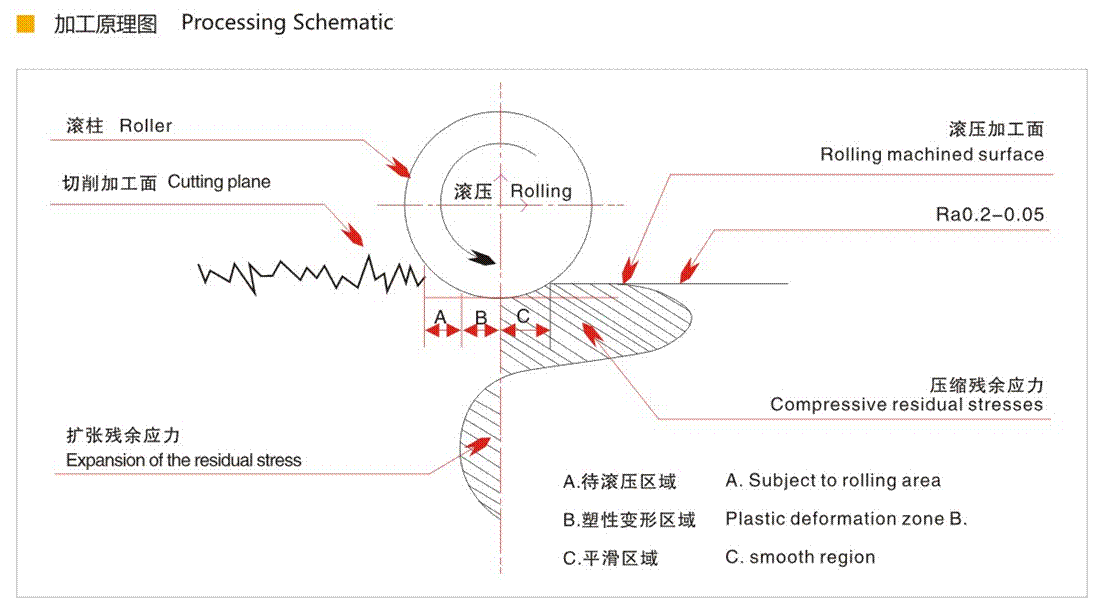
1. Reserve the metal surface with rolling amount, and the surface roughness can be reduced from ra3.2 by one-time fine pressing with rolling tool μ M to 0.4-0.04.
2. It has a fine-tuning device (only applicable to inner hole and outer diameter rolling cutter). Within the appropriate rolling allowance, the size can be controlled within 0.0025mm, and the fine-tuning range can be about 0.5mm.
3. Improve efficiency and reduce cost. The rolling process takes 1 / 10 - 1 / 20 of the grinding process, and the tool clamping can be used on any rotating and feeding equipment (such as turning, milling, drilling, boring machine, CNC lathe, machining center, etc.). The tool is easy to operate (without training professional technicians) and can be used for a long time. Only the rotating parts need to be replaced, and the maintenance cost is low.
4. The surface hardness of the product after rolling can be increased by about HV40, and the fatigue strength can also be increased by about 30%, so as to improve the service life and performance of the product.
5. Roller rolling is only applicable to metal processing within hrc40. Diamond rolling can process workpieces with hardness up to HRC65.
6. Cooling and lubrication shall be carried out during processing, and low viscosity oily working fluid shall be used. Theoretically, it can be processed without lubrication, but considering that it will affect the service life of tools and the surface finish of products, it is recommended to use lubricating fluid( Use oiling cutting fluid on CNC machine tools; When processing steel parts on ordinary machine tools, oil and diesel oil are used, and when processing aluminum parts, oil and kerosene are used, mixed at the ratio of 3:7; Copper parts (sewing oil or 32# transformer oil can be used)
Common knowledge of rolling tools:
1. What is a rolling head (rolling cutter, rolling tool)? How much accuracy can be controlled?
The principle of rolling processing is to flatten the convex part of the metal surface with a high hardness and smooth rolling needle to make the concave part bulge and process it into a smooth mirror like surface, which is different from cutting. It is a plastic processing. While improving the surface roughness in a short time, the surface is work hardened, and a wear-resistant surface is obtained due to the generation of compressive residual stress.
Within the range of reasonable rolling allowance, the dimensional accuracy can be controlled within 0.0025mm.
2. What are the advantages of rolling head machining compared with other surface machining methods?
Compared with other processing methods, rolling has the advantages of high production efficiency, simple and convenient operation, and the surface roughness, surface hardness and wear resistance of the processed workpiece are improved.
3. What machine tool is the rolling tool used on? What are the processing conditions?
It can be used on ordinary lathe, drilling, boring, milling, machining center and other machine tools with convenient clamping. During machining, only one of the tool and workpiece needs to rotate and feed.
The hardness of the workpiece processed by the rolling tool shall be within hrc40. Before rolling, the tool grain on the workpiece surface shall be loose and uniform, and shall not be too deep. It is best to use the point cutting pin processing method such as lathe or boring machine to process it into a regular surface shape. For the irregular machined surface obtained by drilling, the convex part cannot be completely buried into the concave part after rolling, and good surface effect cannot be obtained.
4. Replacement of parts after tool wear
If the parts of the tool are worn, they can no longer be used when they cannot be repaired, such as needle roller, mandrel, retaining sleeve, etc. We all have supporting parts replacement, which is convenient to replace. Note that the needle roller shall be replaced in a complete set.
5. Do you need working fluid for rolling?
Low viscosity working fluid shall be used during rolling processing, and the rolling head shall be cleaned frequently. Oily pin cutting fluid shall be used when it is used on CNC lathe. When it is used on drilling machine, ordinary lathe and other machine tools, oil + diesel shall be used for steel parts, oil + kerosene shall be mixed in the ratio of 3:7 for aluminum parts, and 32# transformer oil or sewing oil shall be used for copper parts.
Theoretically, it can also be processed without lubrication, but it will affect the service life of the tool and the machined surface roughness, so it is recommended to use working fluid.